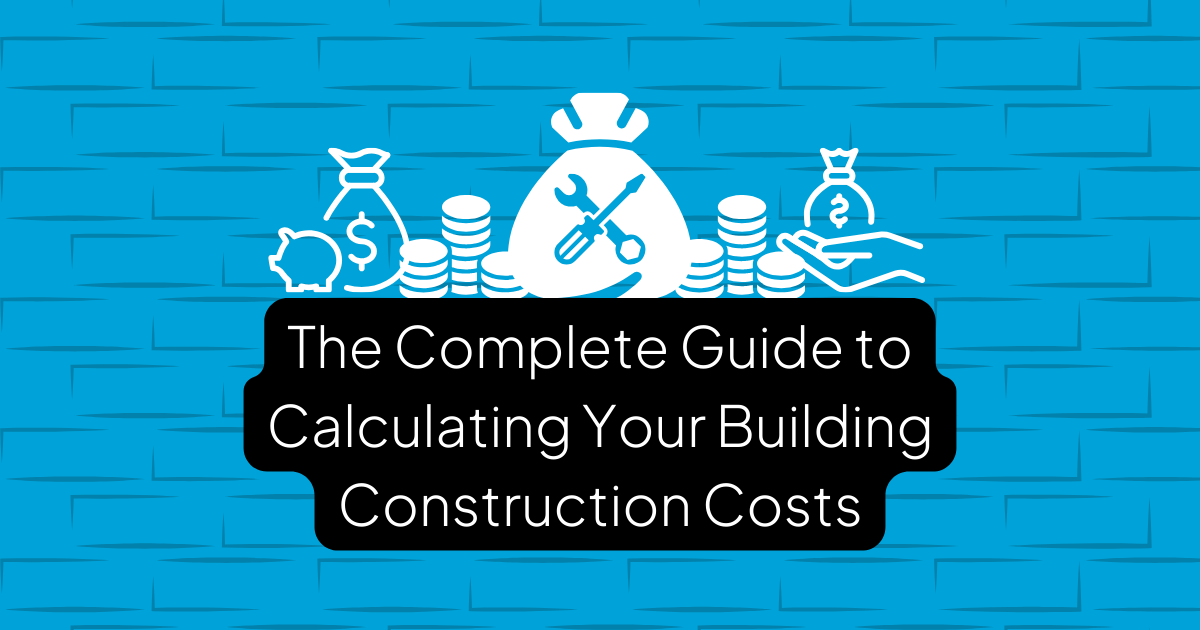
In the last few years, the world has watched the cost of everything go up. In Australia, we feel the pinch of disrupted supply chains; prices from timber to piping have continued to climb, and demand hasn’t slowed down.
Getting construction costs accurate and on budget is as important as ever, but it can be increasingly stressful and fraught thanks to a market that isn’t calming down. Estimates can’t afford to be affected by price blowouts!
The question is how to calculate building construction costs while staying competitive and earning enough to grow your business.
Cost Estimation Challenges
Estimation and quoting can become easier as you gain experience and navigate various jobs, but with that experience, you might find how it can stuff up, too. Estimations are just that: they’re ballpark figures based on current and previous knowledge, but not exact figures. You want an estimate to be close to the final budget figure but give enough wiggle room if something goes wrong.
You’ll come up against the issue of how to calculate building construction costs while leaving room for a profit margin. Remaining competitive while juggling a profit margin and rising costs is difficult, but being upfront is the best place to start.
Breakdown of Building Construction Cost
When figuring out how to calculate building construction costs, there are several major considerations. Some are direct costs, going towards tangible goods and services required for a successful construction project, while others are indirect costs that are nonetheless essential.
It’s important to remember all of these job costs when learning how to calculate building construction cost; you want enough to cover everything and keep your business viable. Overhead is just as vital as direct costs.
So, let's break some down.
The Design
It might be tempting to start at raw materials and land costs, but the cost of design can affect cost estimates and how to calculate a building construction cost, even before anything is ordered.
Houses are a clear example of being cost-effective with design choice, but any construction takes this first step into account. Is the design off-the-shelf or similar enough to other constructions? Or is it a unique design that needs to be accounted for? How unique? As tempting as it is to want a number available immediately, you might need to wrangle with the architect's and the customer's expectations on what is feasible.
Design itself can cause a lot of work preconstruction, which eats into the budget! Preconstruction will land on the budget and costs for the proposed project, so you don’t want to rush it and end up with an unrealistic estimation.
The finishes included in the design stage will increase the average cost, ranging from basic to luxury finishes, which takes us to the majority of building construction costs!
Materials and Storage
When calculating building construction cost, supplies are one of your major pain points. It’s not like the team can build a retaining wall out of dreams and use imagination for nails.
Materials will constitute about 50% of your total costs, and are the largest part of the budget. This means there’s a lot of pressure to get it right. It doesn’t help that costs are going up, and disruption to supply chains can cause knock-on effects that drive up the budget.
With this in mind, always leave a margin for unknowns.
Simple changes to material use can provide huge cost differences, for example:
Timber: $1300 -$1500 per m2
Steel: $1300 - $2000 per m2
Brick (veneer or double): $1600 - $2400 per m2
Another consideration for materials is storage, safety, and transport. With the cost of materials, the last thing you’d like is expensive supplies to go mysteriously ‘missing’ from a work site.
Labour
When considering how to calculate building construction cost, labour is your next significant cost! Construction takes time, and skilled builders are in high demand. This equals a higher overall cost for the project.
A basic labour cost calculation comes down to:
- How many people are working?
- What is their pay rate?
- How many hours will they work?
This ties into the importance of the design. Different contractors and tradies will be needed depending on the size, layout, and materials.
For example, say the project is a timber frame home with brick veneer on a block that needs clearing. A bricklayer for a home build will run anywhere from $50-$100 per hour.
Carpenters can cost from $50-$120. An excavator for the site could be $100-$300.
When calculating the cost of labour, it’s a good idea to have a spreadsheet of everyone necessary for project completion and their projected hourly rates.
Equipment
Everything from vehicles, on-site equipment, electricity, security, port-a-potties, and more will need to be covered in your cost calculations.
What equipment needs to be hired and when? When will it get to the site? This is another spot where detailed design shines, as you can foresee potential equipment costs from the design alone.
Site Works
Even after considering materials, labour, and land, the costs aren’t done. Everything else might be ready to go, but this can add to construction costs when the land is thrown in. Site works are like a bite-sized version of total costs, with similar considerations: location, materials, labour, permits, and land. The customer might be happy with getting a good deal on the land, but cheap land is cheap for a reason, and it’s up to the construction team to bring it up to scratch.
Site works will include testing the soil, determining the land's connections (water/sewage/electricity,) removing debris/trees, and ensuring termite protection and security.
A small, relatively flat piece of land can run about $5000 in site work costs.
$10,0000 - $15,000 is closer to the average quote for a medium site. The larger the land, the more expensive.
A large piece of land, or sloped land, can run about $25,000 for site work.
As with all considerations when calculating building construction cost, add a buffer to ensure you are prepared for any unforeseen expenses.
Permits
The necessary permits and approvals for any build need to be researched as part of the preconstruction process.
This is especially important for the construction of commercial or industrial buildings, as there will be different regulations and requirements depending on the intention of the construction.
Cost varies depending on location, council, and intended land use.
Weather and Natural Disasters
It’s an absolute pain: all the materials have arrived, everyone’s on-site, and they’re even ready to work. Then you get heavy rain and get washed out for the day. This is more of a time consideration, but as time is money, Natural disasters can’t be foreseen or always accounted for, but for building in certain areas, you’ll need to account for the local weather and chance of disaster.
Such as a bushfire-prone area! Construction must be done during certain times of year to comply with fire bans or hot weather. Supply storage could be remote or need higher consideration to prevent damage. Areas with flooding are similar: will the construction be different for flooding considerations? Is the site unsuitable for construction without design changes?
It’s important to remember these when deciding how to calculate building construction costs.
Insurance and Liability
All tradies should be covered by insurance to protect themselves from accidents and unforeseen circumstances. It’s not just to cover the direct cost but any run-on costs from delays or damage. Insurance is a requirement for construction projects to ensure protection for the project and business because you can never be sure what could happen!
Builders insurance can be obtained for specific projects or as a yearly plan. Insurance for construction works covers losses incurred by damage or accidents. There are many reputable plans out there for any tradie.
How to Calculate Building Construction Cost
Keeping in mind our above construction costs and considerations, we can have some cost assumptions, as we can’t know for sure exactly what everything will cost. Our assumptions are based on the design, materials, and standard labour and conditions. The more info on your construction pricing, the better.
We can either consider the overall cost or the cost per square metre. Cost per square metre is often more popular as it can be scaled depending on the project size.
The overall construction cost will be the cost per square metre (SQ) multiplied by the project size (P).
SQ x P = Cost of Construction
Prices for Calculations
The average home construction price in Australia is between $1300 to $4000 per square meter. These costs are based on all the factors covered above.
For example, the figures for a custom-designed house:
-Basic rate, including basic finishes, flat site, and inexpensive materials such as timber: $1200 - $1500 per square meter
-Standard rate, including quality finishes, flat site, and materials such as brick veneer: $1800 per square meter
-Luxury rate, including high-quality finishes, flat site, and expensive materials such as double brick: $2100 per square meter
These rates can go even higher with add-ons such as:
-Garages: $1200 per square meter
-Decks/Verandahs: $900 per square meter
Or with consideration of the land and site work needed. A difficult site can be upwards of 20% of the additional cost.
Construction Cost Calculators: Are They Accurate?
Figuring out how to calculate building construction costs is a skill; it takes time, experience, and the knowledge of many people in the construction industry.
Construction cost calculators help get a ballpark on your estimates and give you a reasonable idea of what the final price is. Calculators are developed with general prices in mind, including your overhead.
What to Charge Upfront
Most construction projects will ask for a deposit upfront. This is to cover the initial costs of construction, cover overhead to prepare and act as a guarantee of sorts that the client is locked in.
Typically, builders will charge about 20% of total construction cost as a deposit. Further payments are up to your discretion, but it’s important to cover costs as you continue the build. Being upfront with your expectations is important, and they need to be locked into any contract.
Building Success with Cost Estimator Software
As you can see, accurate costing can be an absolute pain. It’s necessary to be able to refine a budget, keeping all your overhead in consideration while also remaining competitive in your pricing. Experience helps, but costs fluctuate, and every work site is different!
With plenty of moving parts, making use of job estimating software and tools can be a lifesaver: keep all your prices, spreadsheets, permits and more in one handy place. With software like AroFlo, have everything you need directly on your device, so it works with you and goes with you, no matter the job site.